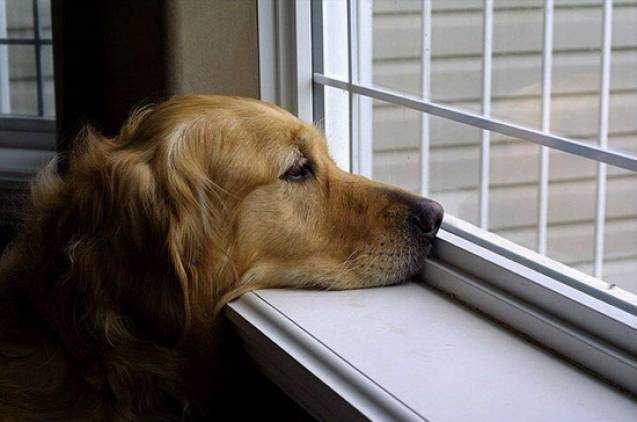
We’re so impatient. Trust me, I’m the worst in that regard. Though ironically I’m perfectly suited for this job because I aim my shepherding powers directly at the vendors, service providers and manufacturers I work with on behalf of clients.
There’s a reason everything takes so long and I’m going to tell you why, in painful detail. The good news is, if you work with us, you’re not subject to any of it, except of course, the patience.
Although it’s not funny, I giggle amusingly that the more you pay, often the longer you’ll have to remain patient. It’s ok, it’s always worth it in the end.
Planning 101 – Pay Now or Pay Later
[WPGP gif_id=”5583″ width=”600″]
Years ago, I had a colleague who always said this. For all the effort you don’t put in the beginning of any endeavor, you’ll pay dearly later during the chaos and scrambling to make it right.
Along those lines, we front load so much work in the beginning of each project. Trades have eyes on the “before” space well in advance of continuing to dive into the design process, which itself can take weeks or months. This way, trades have immediate and valuable context when they provide estimates based on real-life, not theoretical visualizations.
We have to be a nag when it comes to checking in on orders. Fortunately that’s a role that’s natural for me.
And further, when we present the design, it’s all at once. One fell swoop. All right in front of you, and we’ve checked stock and lead times on everything before showing it. More later on that averted disaster.
I have this horrible aversion to procrastination. I was the one of those students who had his term paper done days or weeks in advance. The mania generated from last-minute all-nighters hampered — not enhanced — my mojo.
Decisions
[WPGP gif_id=”5585″ width=”600″]
My presentations leave very little decision making left hanging out there. This one is a biggie and I nip it in the bud early on. To me this one seems obvious, if someone can’t make a decision on a particular element, then it follows that every step to the finish line that depends on that will be delayed. So don’t make up your mind, I’ll make it up for you.
Ordering Process
This is a bit how the sausage is made, but it’s under-appreciated for sure and it’s easy to explain.
Let me paint a colorful picture. As part of the design, we specify two lovely custom sofas covered in a sumptuous velvet, adorned with trims, perhaps delicate tufting, plump down-wrapped cushions, a contrast welt, topped off with throw pillows with their own adornments. It’s beautiful, you get it.
Every order is just a promise.
I estimate that to make that a reality, we’ll generate maybe eight to ten purchase orders, to different vendors with different shipping addresses and maybe a stopover at a textile finishing company to knit-back and stain protect the beautiful fabric.
What could possibly go wrong?? Oh, I don’t know, here’s a few ideas. Maybe the fabric we fell in love with arrives damaged. Well, can the workroom cut around it? No, of course not, we’ll need another four yards. What, there’s only two yards left in stock? End of August? Then two more weeks to knit back and stain protect?
And that’s just the fabric. It’s laughable really, but we plan for these scenarios. It’s our job to keep the plates spinning.
Mobility, Permitting and Schedules
Renovations require the same vigilance and foresight. As we explored in a recent blog post, “Demo now, design later” doesn’t quite work. And a fine builder won’t allow it.
Days or weeks leading up to the start of a remodeling or new construction project, there’s an array of tasks that need to be in order, including set up, protection, aligning trade schedules and most importantly, securing permits.
Imagine the potential for delay without a solid plan in place, which includes a well thought-out design and review of the project requirements.
ON UPDATE CASCADE
If you get this reference, you’re a database nerd. It holds true and is a great analogy for keeping everything and everyone on a project in sync.
It generally means that if you change one seemingly harmless thing and there are references to it in other areas, that it must be changed in every other instance. Modern databases do this for us automatically, but projects aren’t databases.
Imagine the design is complete, ordering has begun, maybe construction is underway.
“Can we just move that sink over nine inches?”
Well, during the design process, we can control the cascading effect of a simple request like this, on paper. The consequences of a change like this after the fact could — at best — require a complete redesign of a kitchen configuration. And at worst, after cabinets have been ordered, rough plumbing has been set and appliances are on their way, begin to scramble!
Delays
Every order is just a promise. And we use each promise to line up everyone’s schedules. But in reality, delays happen. And a delay in the smallest component can affect the critical path of a project.
We have to be a nag when it comes to checking in on orders. Fortunately that’s a role that’s natural for me: “Is it here yet? Are we still on track? Are we sure they are not awaiting information from us?”
Defects, Quality Assurance and Accidents
Remember all those purchase orders we submitted for the pair of sofas? We ensure each component that arrives does so in pristine condition and no parts are missing!
Picture that chandelier that was sourced from Italy, embellished in hand-blown Murano glass, each stem and hanging bauble its own work of art. So surprised even how quickly it arrived, so it lay on a shelf for weeks or months, unopened, but safe. Until the day the electrician arrives.
Do you like being on the phone with an Italian shop owner for two hours translating ‘broken’ and ‘replacement’ (hoping it’s not in August)? No, most people would rather enjoy a leisurely root canal.
Aren’t you relieved that, with us, you needn’t worry about any of this?
Like what you’re reading? Stay in touch with monthly (or so) e-mails.